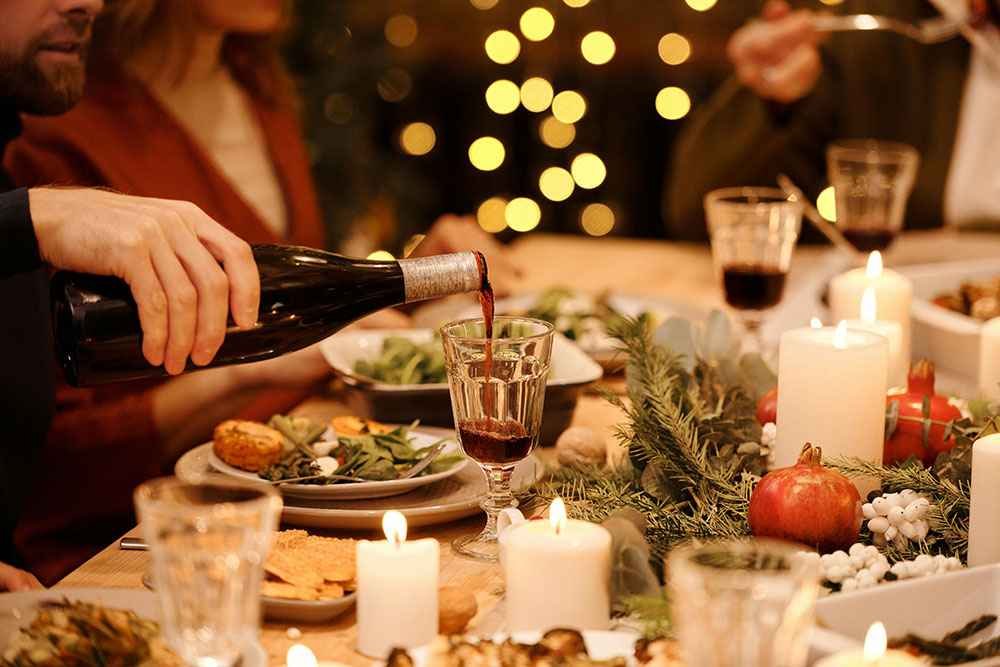
Pourers play a crucial role in various industries, from bars and restaurants to manufacturing and chemical processing. These small yet vital devices ensure a controlled and precise flow of liquids, impacting both the quality of the final product and operational efficiency.
In this article, we will delve into common pourer problems, providing in-depth insights into their causes and offering practical solutions. Additionally, we’ll explore maintenance tips to help extend the life of pourers, ensuring they consistently deliver pouring perfection.
Common Pourer Problems
Drip Issues
Drips during pouring can be a persistent annoyance and can lead to wastage, affecting both customer satisfaction and operational costs. The primary cause of drips is often an incorrect pouring angle.
When the liquid stream hits the glass at an improper angle, it can result in unwanted drips. To address this, bartenders and staff should be trained to pour at the optimal angle, minimizing drips and enhancing the overall customer experience.
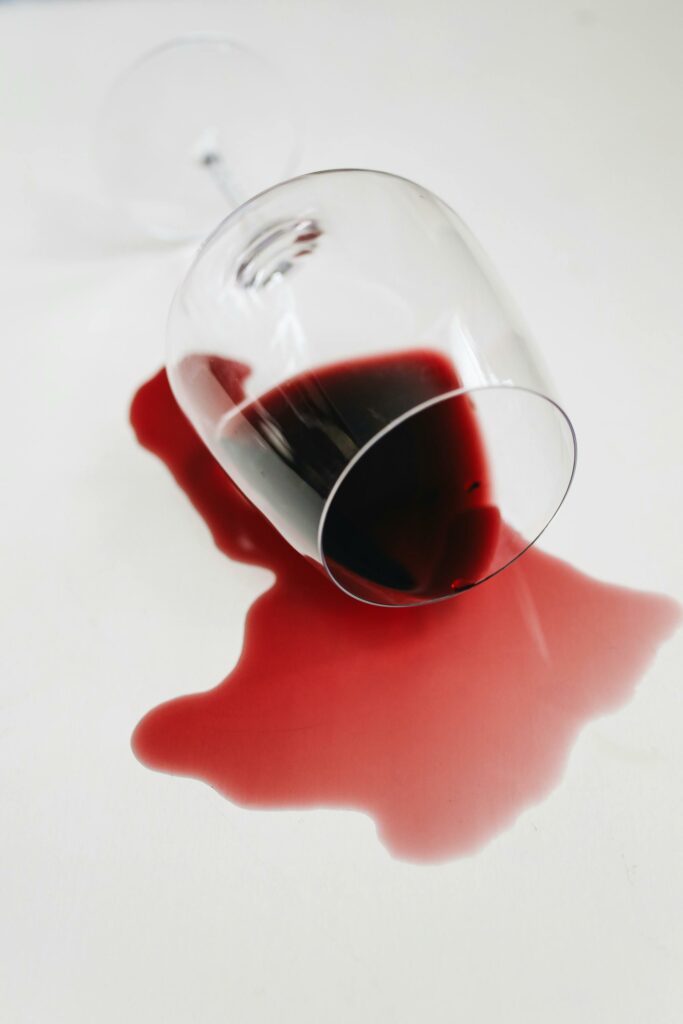
Inconsistent Pouring
Inconsistent pouring can stem from various issues, including pourer calibration problems or the use of damaged pourers. Calibrating pourers correctly ensures a consistent flow rate, preventing under-pouring or over-pouring.
Additionally, identifying and replacing damaged pourers is crucial to maintaining a reliable pouring experience. Regular staff training on calibration techniques and recognizing pourer damage can significantly mitigate inconsistent pouring issues.
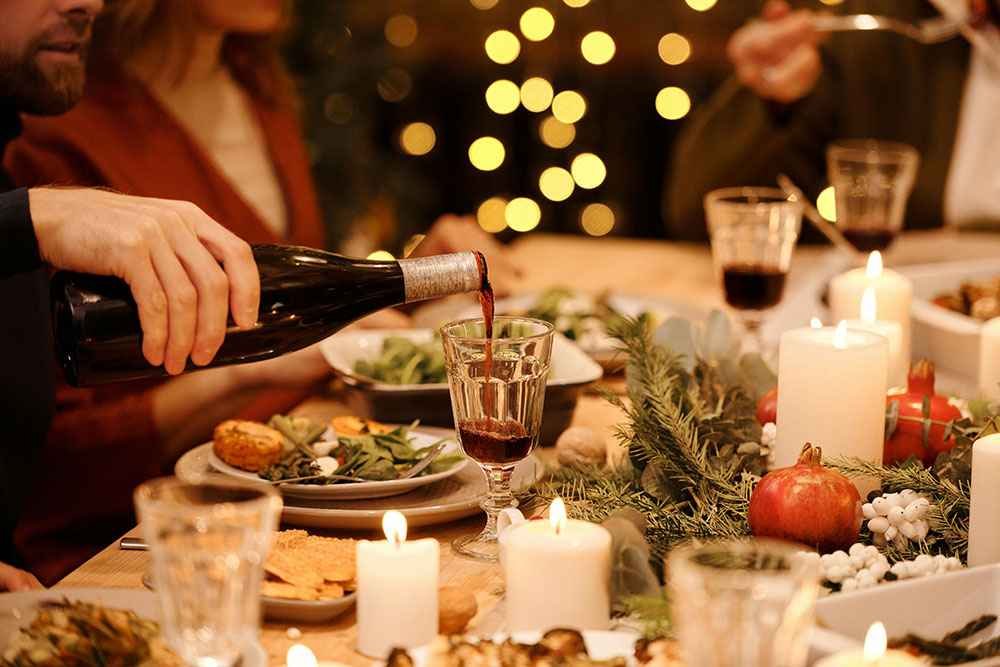
Leakage Problems
Pourer leaks not only lead to product wastage but can also pose safety concerns and damage to equipment. Loose pourers are a common cause of leaks, and tightening them regularly is a simple yet effective solution.
Moreover, routine inspections should be conducted to identify any potential leaks early on, allowing for timely repairs or replacements. By addressing leakage problems promptly, businesses can avoid operational disruptions and potential hazards.
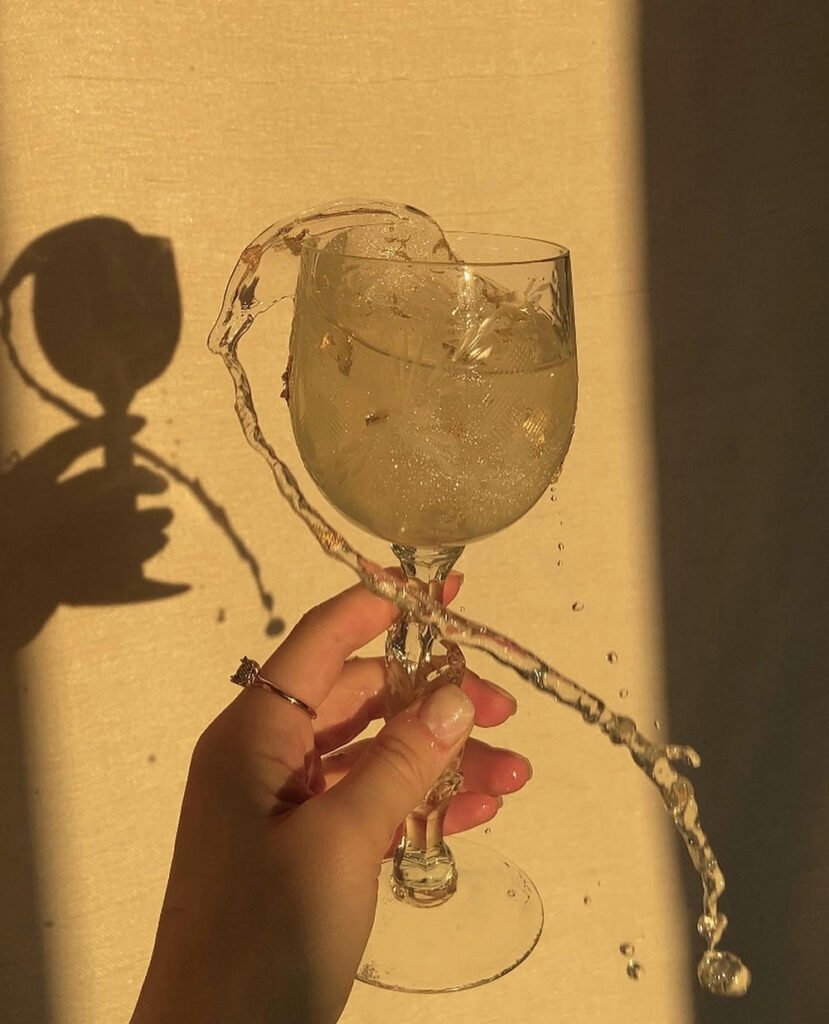
Clogging Challenges
Clogging in pourers can occur due to the accumulation of debris or dried liquids. Regular cleaning practices, including disassembling pourers for thorough cleaning, can prevent clogging and ensure a smooth flow of liquids. Using pourer caps when not in use can also be an effective measure to prevent debris from entering the pourer spout. Choosing pourers designed for specific liquids can further reduce the likelihood of clogging issues.
Troubleshooting Solutions
Drip Issues
- Adjusting Pouring Angle – Training staff to pour at the optimal angle minimizes drips and enhances customer satisfaction. Encourage a consistent pouring technique to reduce variations in the pouring process.
- Selecting the Right Pourer Type – Different pourers are designed for various types of liquids. Choosing the right pourer type for specific beverages can prevent issues like drips and ensure a controlled pour.
- Regular Cleaning Procedures – Incorporate regular cleaning routines into the operational workflow to prevent the buildup of residues that could contribute to dripping. Use appropriate cleaning solutions and tools for effective maintenance.
Inconsistent Pouring
- Calibration Techniques – Implement regular calibration checks to ensure pourers maintain a consistent flow rate. Provide staff with training on proper calibration procedures and the importance of maintaining accurate pour volumes.
- Identifying and Replacing Damaged Pourers – Educate staff on recognizing signs of pourer damage, such as cracks or wear. Establish protocols for the prompt replacement of damaged pourers to maintain consistency in pouring.
- Ensuring Proper Installation – Improper installation can lead to pourer issues. Emphasize the correct installation of pourers to prevent leaks or inconsistent pouring. Provide visual guides or training materials for reference.
Leakage Problems
- Tightening Loose Pourers – Regularly check and tighten loose pourers to prevent leaks. Implement a schedule for routine inspections to identify and address loose pourers promptly.
- Seal Replacement – If leaks persist, consider replacing pourer seals. Educate staff on the importance of intact seals and provide guidance on the replacement process.
- Routine Inspections for Early Detection – Establish a regular inspection routine to detect potential leakage issues before they escalate. Include pourer inspections in preventive maintenance schedules to ensure ongoing reliability.
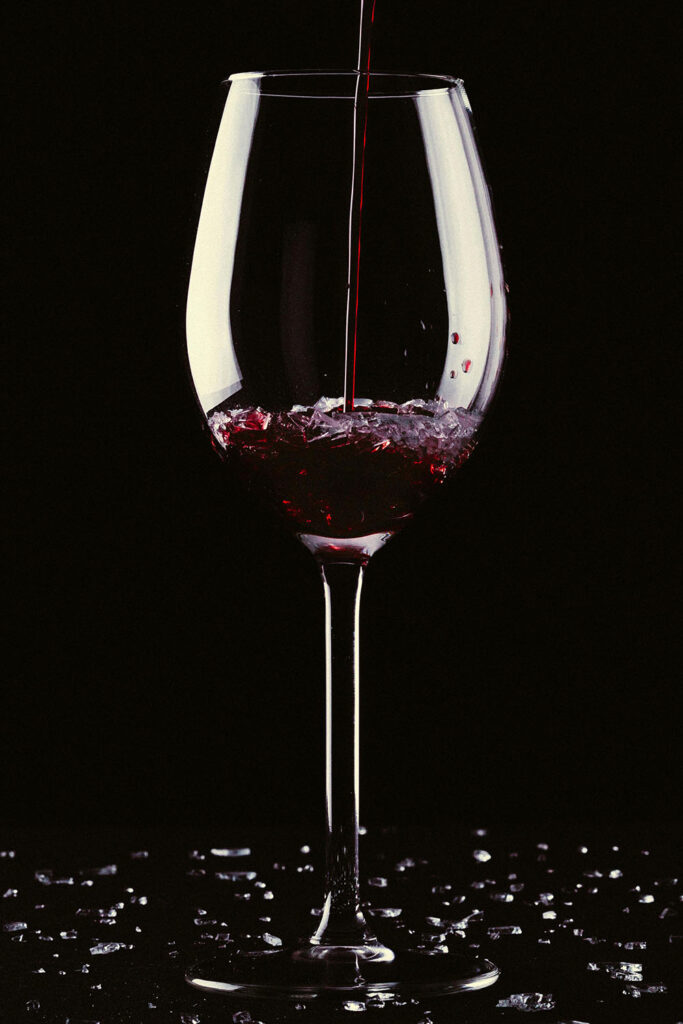
Clogging Challenges
- Regular Cleaning Practices – Promote regular cleaning practices to prevent clogs. Provide staff with guidelines on disassembling pourers for thorough cleaning and encourage adherence to cleaning schedules.
- Using Pourer Caps – When pourers are not in use, utilize pourer caps to protect against debris and contaminants. This simple measure can significantly reduce the likelihood of clogging issues.
- Choosing Pourers Suitable for Different Liquids – Consider the viscosity and characteristics of the liquids being poured when selecting pourers. Choosing pourers designed for specific liquids can prevent clogs caused by mismatched pourer and liquid properties.
Maintenance Tips for Extended Pourer Life
Cleaning Frequency
Regular cleaning is paramount for pourer maintenance. Establish a cleaning schedule based on usage intensity, with more frequent cleaning for high-volume settings. Utilize appropriate cleaning solutions and tools to ensure thorough cleaning.
Storage Practices
Proper storage is essential for preventing pourer damage. Store pourers in a cool, dry place away from direct sunlight and extreme temperatures. Consider using protective covers or containers during non-use periods to prevent accidental damage.
Inspection Routines
Implement regular inspection routines to identify wear and tear signs early on. Train staff to recognize common issues during inspections and address them promptly. Proactive measures can prevent more extensive problems and extend the overall lifespan of pourers.
Educating Staff and Users
Training Programs for Staff
- Importance of Staff Awareness – Emphasize the significance of staff awareness regarding pourer issues. Educate staff on how pourer problems can impact operations, customer satisfaction, and overall efficiency.
- Incorporating Pourer Maintenance in Training – Integrate pourer maintenance into staff training programs. Provide comprehensive training on troubleshooting common pourer issues, calibration techniques, and proper installation procedures.
- Addressing Pourer Issues Promptly During Operations – Encourage a proactive approach to pourer issues during daily operations. Empower staff to address pourer problems promptly and efficiently to minimize disruptions and ensure a seamless customer experience.
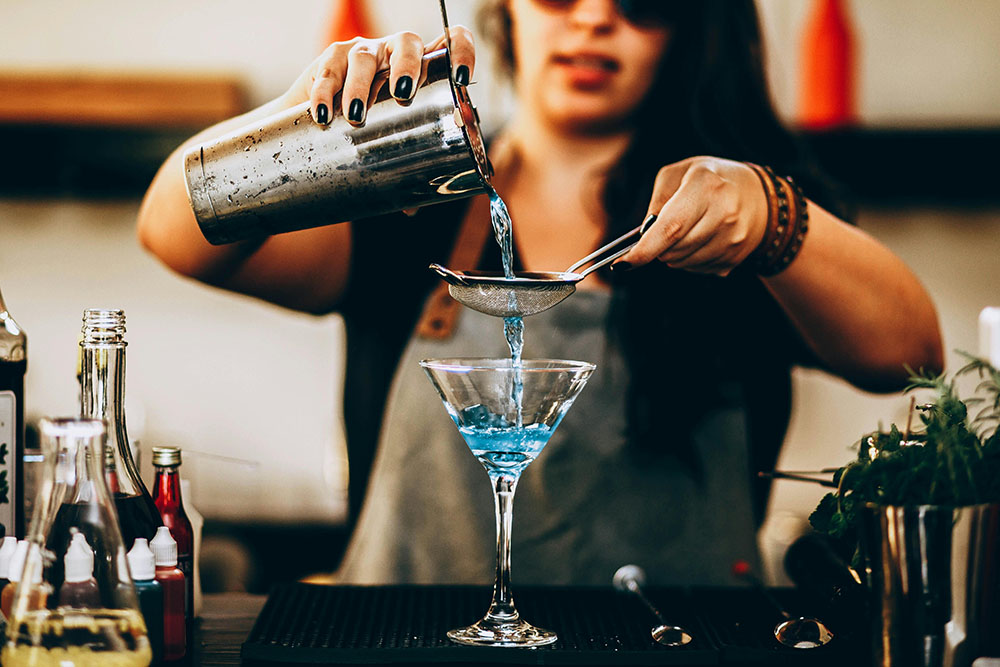
Customer Education
- Providing Information on Proper Pouring Techniques – Offer information to customers on proper pouring techniques, especially in self-service settings. Display signage or provide pamphlets explaining the optimal pouring angle to reduce drips and spillage.
- Encouraging Feedback on Pourer Issues – Create avenues for customer feedback on pourer issues. Encourage patrons to report any problems they encounter, fostering a collaborative effort to maintain pourer functionality.
- Collaborative Efforts for Improved Pourer Performance – Forge partnerships with suppliers and manufacturers to enhance pourer performance collaboratively. Provide feedback on pourer issues and work together to develop improved pourer designs and technologies.
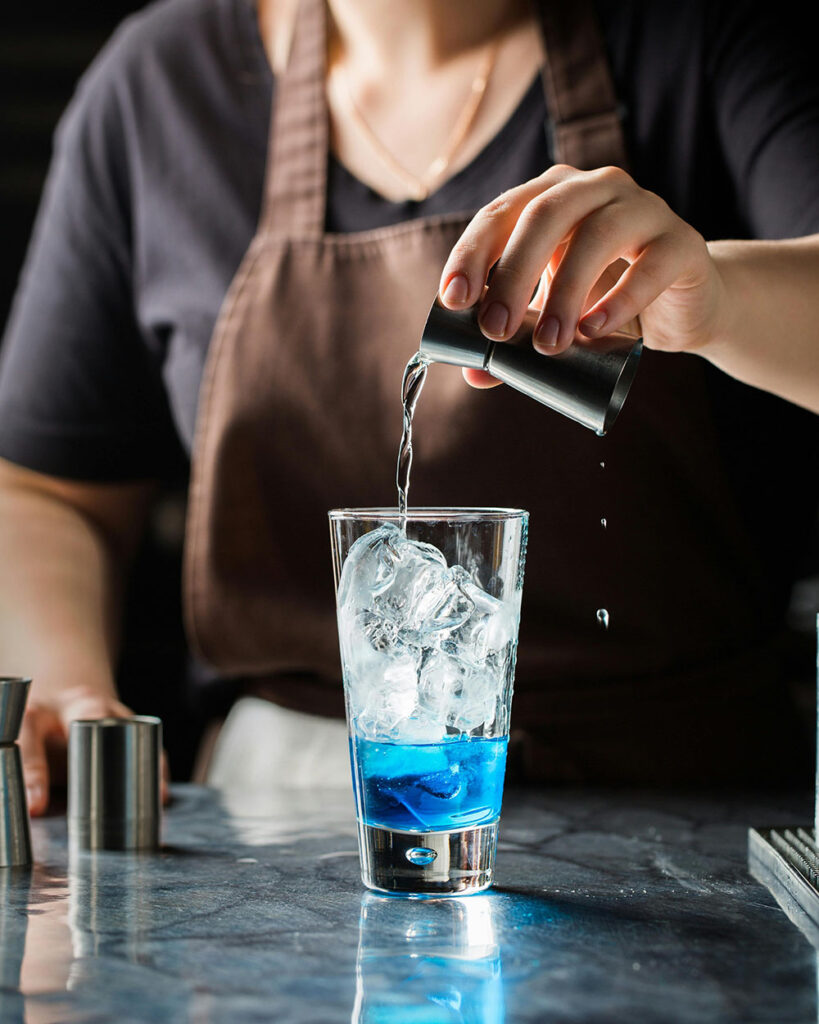
Proactive Pourer Solutions
In conclusion, addressing common pourer problems requires a combination of proactive troubleshooting, regular maintenance, and comprehensive education for both staff and users. By understanding the causes and solutions for drip issues, inconsistent pouring, leakage problems, and clogging challenges, businesses can optimize pourer performance and ensure pouring perfection.
Implementing troubleshooting solutions and maintenance tips, coupled with educating staff and customers, creates a holistic approach to extend the life of pourers, promoting efficiency, cost-effectiveness, and customer satisfaction in various industries.